A Preventative Maintenance Cornerstone
As a universal industry practice, having your transformer oil routinely tested is an indispensable part of a preventative maintenance program. A transformer oil analysis allows you to monitor your equipment condition while detecting potential issues. During the transformer oil analysis, we monitor the oil’s water content, contamination, acidity, power factor, and dielectric strength in order to identify issues before they result in equipment failure.
With a routine transformer oil analysis, we monitor your oil on the following factors to preemptively identify issues before they result in equipment failure.
Moisture Content: High moisture reduces the oil's insulating properties, resulting in equipment performance and a dialectic breakdown.
Acid Number: High acid causes oil to sludge, resulting in blocked oil canals.
Dielectric Strength: A reduction in dielectric strength indicates that the oil is no longer providing electrical insulation effectively.
Liquid Power Factor: A high power factor indicates significant power loss within the oil.
Dissolved Gas Analysis: Varying levels of combustible gases in the oil indicate faulty operational or equipment problems. These gases include nitrogen, oxygen, carbon monoxide, hydrogen, methane, etc.
Furans: Measuring furans helps identify the level of degradation within the cellulose paper.
Benefits of a Transformer Oil Test:
- Determines the condition of the equipment
- Ensures equipment reliability
- Reduces downtime and repair costs
- Maximizes the life expectancy of the equipment
- Identifies excessive overheating, overloading, arcing, and suddenly occurring faults
- Detects loose connections, badly butted joints, and paper insulation embrittlement
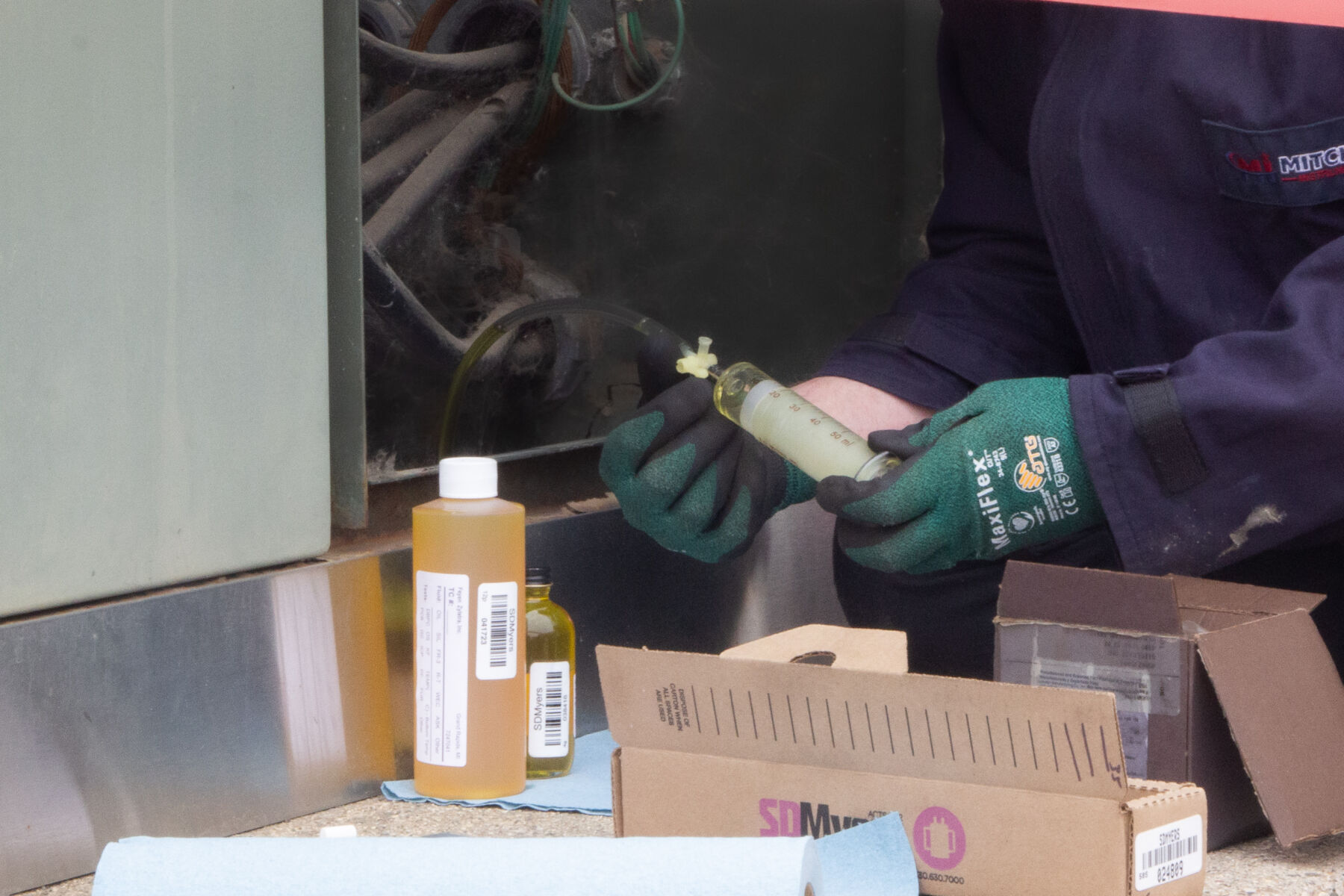
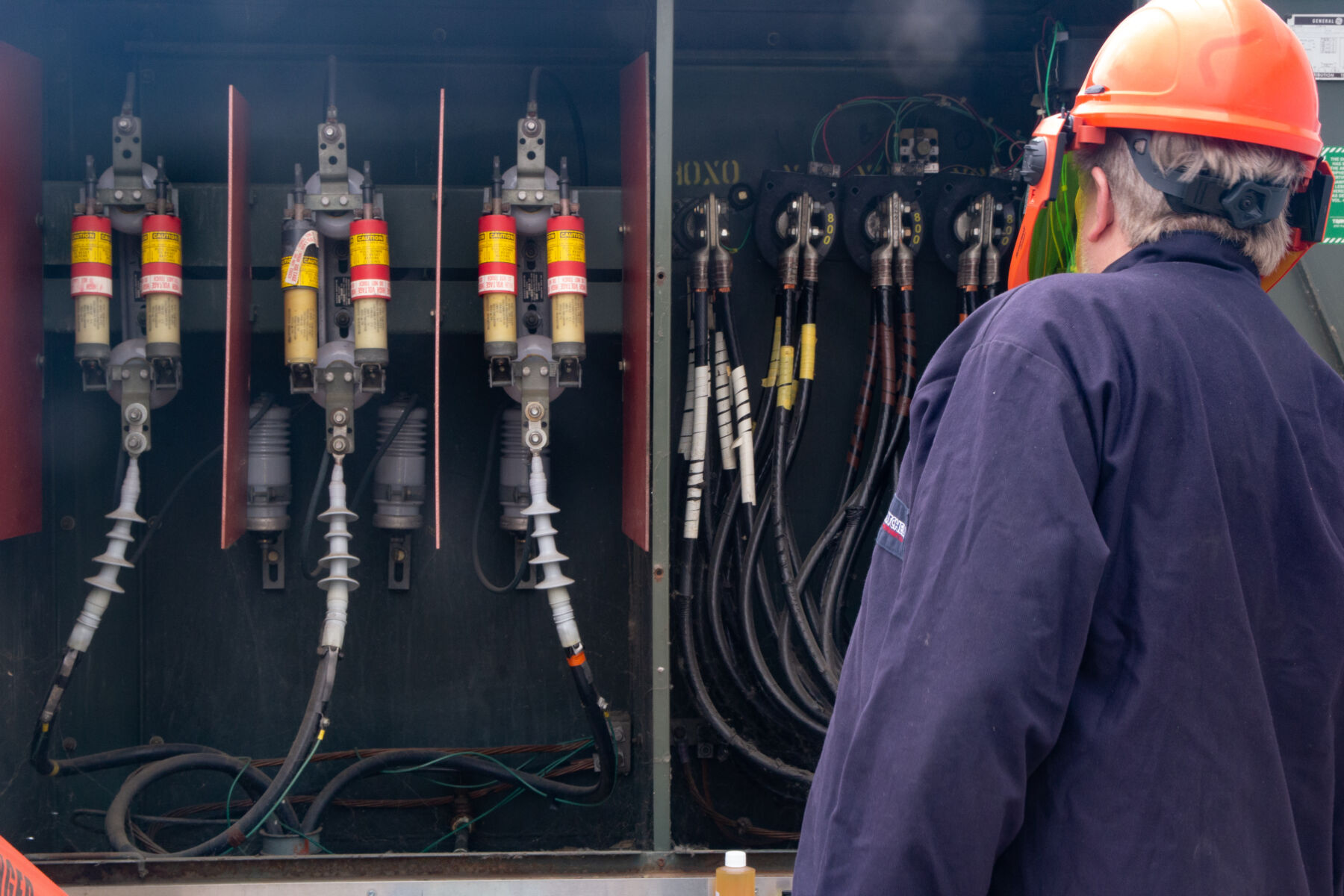
We recommend that your transformer oil should be tested periodically:
- General and Physical Tests: Every 6 Months
- Dissolved Gas Analysis: Every Year
- Furan Testing: Every Two Years